Best Practices for Implementing Manufacturing Factory Automation Solutions
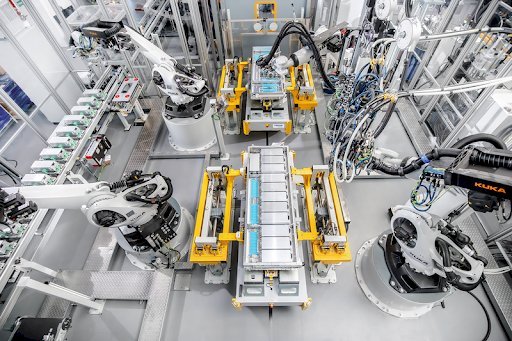
Introduction
Implementing factory automation solutions is fundamental for further developing efficiency, quality, and proficiency in manufacturing. Following best practices guarantees a smooth progress and expands the advantages of automation innovation.
Outline
Introduction
Background
Best Practices for Automation Execution
Normal Traps to Stay away from
Conclusion
FAQs
Background
Factory automation includes coordinating innovations like mechanical technology, IoT, and high level programming to smooth out manufacturing processes. Legitimate execution can prompt critical additions in efficiency and cost decrease yet requires cautious preparation and execution.
Best Practices for Automation Execution
Evaluate Current Cycles and Needs
Direct an intensive investigation of existing work processes and recognize which regions can benefit most from automation. Understanding explicit necessities helps in choosing the right automation solutions.
Characterize Clear Targets
Put forth quantifiable objectives for the automation project, for example, expanding creation yield, working on quality, or lessening costs. These targets guide the execution interaction.
Pick Versatile Solutions
Select automation advancements that can develop with your business. Versatile systems consider future extension and updates without critical disturbance.
Representative Preparation and Commitment
Give far reaching preparation to representatives on the best way to work with computerized systems. Drawing in staff almost immediately limits opposition and assists them with adjusting to new advancements.
Begin Little and Scale Bit by bit
Start with robotizing a solitary cycle or region before growing to different tasks. This limits risk and permits time for tweaking and resolving any issues.
Customary Upkeep and Checking
Execute an upkeep plan to keep computerized systems running effectively. Customary observing guarantees any issues are immediately distinguished and settled.
Normal Entanglements to Stay away from
Disregarding return on initial capital investment Investigation
Neglecting to work out the profit from speculation can prompt spending on pointless innovation. Continuously assess expected monetary advantages before implementing automation.
Over-Automation
Mechanizing each cycle isn't generally the best methodology. Center around regions where automation offers the most benefit and keep up with manual control where essential.
Ignoring Workforce Reconciliation
Ignoring representative preparation can bring about low reception and functional failures. Guarantee legitimate preparation is given all through the change to automation.
Conclusion
Implementing factory automation requires an essential methodology, from evaluating current necessities to giving staff preparation. Following best practices guarantees the effective sending of automation solutions, augmenting efficiency, and keeping away from normal entanglements.
FAQs
1. For what reason is it critical to survey current cycles before mechanizing?
Evaluating current work processes recognizes regions that would benefit most from automation, guaranteeing that assets are apportioned really.
2. Which job does representative preparation play in automation execution?
Preparing guarantees that workers are prepared to utilize robotized systems effectively, prompting smoother incorporation and less opposition.
3. Should all cycles be robotized immediately?
No, it's best to begin small and scale step by step. Mechanizing each region in turn decreases risk and considers changes before extending further.
4. How could over-automation be kept away from?
By zeroing in on mechanizing undertakings that give the main advantages and holding manual control where automation doesn't add esteem.
5. What is the significance of standard upkeep in automation?
Ordinary upkeep guarantees that mechanized systems run proficiently and recognizes and fix issues before they influence efficiency.
What's Your Reaction?


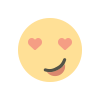



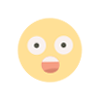