CNC Milling vs. CNC Turning: Key Differences and Use Cases
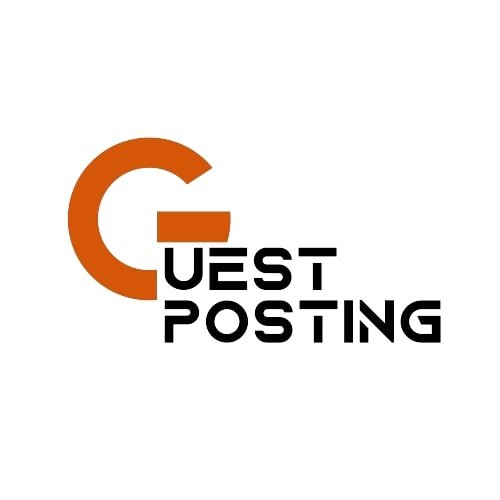
CNC milling and CNC turning are two of the most commonly used subtractive manufacturing processes in modern machining.
While they share core technologies like computer numerical control and precision cutting tools, they differ in part geometry, tool movement, and optimal use cases.
Understanding the distinctions between these two processes helps engineers and manufacturers choose the best method for any given part—whether it's a high-precision aerospace bracket, a cylindrical shaft, or a custom medical component.
What Is CNC Milling?
CNC milling uses rotating cutting tools to remove material from a stationary workpiece.
The workpiece is typically clamped to a machine bed or table, and the cutting tool moves along multiple axes (X, Y, Z, and sometimes A/B for 4- or 5-axis mills). The machine shapes the part by selectively removing material to match the CAD model’s geometry.
Common CNC milling features:
-
Flat surfaces
-
Slots and pockets
-
Complex 3D shapes
-
Angular cuts
-
Threaded holes (with tapping)
Milling machine types:
-
3-axis milling machines – Ideal for basic geometries
-
4-axis and 5-axis milling centers – Handle more complex geometries without repositioning
-
Vertical and horizontal mills – Chosen based on setup efficiency and part orientation
What Is CNC Turning?
CNC turning involves rotating the workpiece while a stationary cutting tool removes material.
This process is perfect for producing parts with rotational symmetry, such as shafts, bushings, and threaded rods.
The workpiece is mounted on a spindle and spun at high speeds. The cutting tool moves linearly to shave off layers of material, typically along the X and Z axes.
Common CNC turning features:
-
Cylindrical or conical shapes
-
External/internal threads
-
Grooves and undercuts
-
Bores and tapers
-
Smooth surface finishes (Ra < 0.8 µm)
Explore CNC turning services if you're machining high-precision round parts or producing components with consistent diameter requirements.
Key Differences Between CNC Milling and CNC Turning
Feature | CNC Milling | CNC Turning |
---|---|---|
Motion Type | Tool rotates, workpiece stationary | Workpiece rotates, tool stationary |
Best For | Flat, complex, multi-surface parts | Cylindrical, round, symmetrical parts |
Axes of Movement | 3 to 5 axes | Typically 2 axes (X, Z); multi-axis available |
Geometry Type | Irregular profiles, slots, pockets | Shafts, rods, threads, round features |
Tolerances Achievable | ±0.01 mm or better | ±0.005 mm or better |
Surface Finish | Depends on tooling and speed | Smoother finish due to rotation |
Setup Complexity | Higher for complex parts | Simpler for symmetric shapes |
Cycle Time Efficiency | Moderate | Fast for round parts |
Use Cases for CNC Milling
CNC milling is ideal for parts with complex geometries or multi-surface features that can’t be achieved with a single-axis lathe.
Typical milling applications include:
-
Aerospace brackets with multiple mounting points
-
Medical implants like bone plates and surgical instrument handles
-
Automotive parts such as engine housings, brackets, and mounts
-
Consumer electronics casings made from aluminum or plastic
-
Tool & die components that require intricate contours and cavities
Milling’s versatility makes it the go-to process for both prototyping and low- to mid-volume production of intricate parts.
Use Cases for CNC Turning
Turning is optimal for parts with rotational symmetry or parts that are long, slender, and designed to spin.
Typical turning applications include:
-
Shafts, axles, and pins
-
Bushings, sleeves, and spacers
-
Threaded rods and fasteners
-
Medical screws or bone implants
-
Hydraulic or pneumatic fittings
-
Valve stems and couplings
CNC turning machines (also called lathes) are extremely efficient for producing these types of components quickly, with minimal material waste and high dimensional consistency.
Multi-Tasking Machines: Combining Milling and Turning
In many modern shops, hybrid CNC machines combine milling and turning capabilities into a single setup.
These multi-tasking machines allow for both tool rotation and part rotation, enabling more complex parts to be machined without repositioning.
This is especially useful for:
-
Parts that have both round and flat features
-
Components that need high concentricity and tight tolerances
-
Reducing setup time and part handling
While multi-tasking machines can be more expensive, they increase efficiency, part accuracy, and overall throughput.
Surface Finish and Tolerance Considerations
Both processes can achieve tight tolerances, but CNC turning typically offers better surface finishes on round parts due to the constant rotational motion and smoother cutting path.
Parameter | CNC Milling | CNC Turning |
---|---|---|
Surface Finish | Ra 0.8–3.2 µm | Ra 0.4–1.6 µm |
Tolerance Range | ±0.01–0.05 mm | ±0.005–0.02 mm |
For extremely smooth finishes (Ra < 0.4 µm), additional processes such as grinding or polishing may be applied after machining.
Cost Considerations
Costs vary depending on:
-
Material type (aluminum is cheaper than titanium)
-
Setup complexity (multi-axis setups take longer to program)
-
Tooling needs
-
Quantity (economies of scale apply)
CNC Milling Costs:
-
Higher for complex parts with 4- or 5-axis setups
-
Cost-effective for low to mid-volume production
-
High upfront programming cost offset by long-term versatility
CNC Turning Costs:
-
Lower setup time and faster cycle times
-
Ideal for high-volume, repeatable production
-
Less programming complexity than milling
For many projects, the best value comes from matching the process to the geometry and end-use of the part.
When to Choose Milling, Turning, or Both
Choose CNC Milling If:
-
Your part has complex surfaces or holes on multiple faces
-
You need tight flatness or perpendicularity
-
The design includes pockets, slots, or irregular contours
Choose CNC Turning If:
-
Your part is round or symmetric along a central axis
-
Threading, boring, or grooving is required
-
You want the fastest path to mass-producing cylindrical components
Choose Both If:
-
Your part has flat faces and cylindrical features
-
You require minimal runout and high concentricity
-
You’re producing parts with complex end caps, flanges, or stepped profiles
Final Thoughts
Both CNC milling and turning are essential machining processes—each with their strengths.
Choosing between them depends on your part geometry, surface finish requirements, production volume, and budget.
Understanding their differences ensures better design decisions, lower costs, and faster lead times.
If you’re unsure which method suits your part, consult a qualified CNC turning service provider who can assess your CAD files and help you select the most efficient and cost-effective solution.
What's Your Reaction?


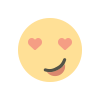



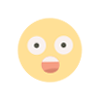