Complete Guide to Loader Electrical Systems & Maintenance
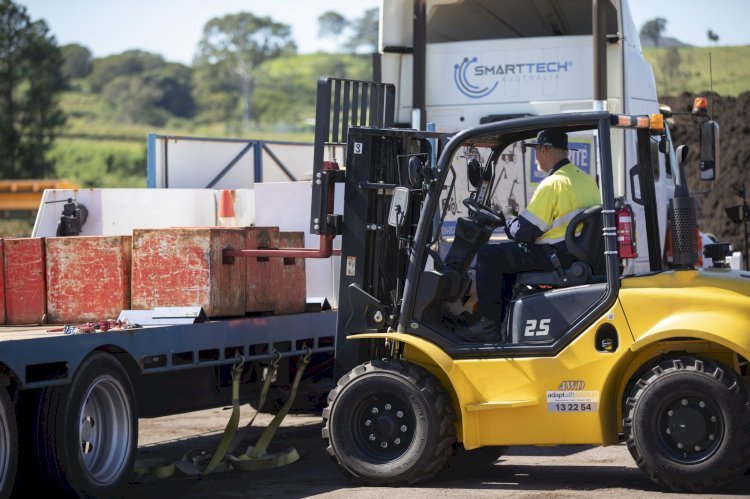
In the world of heavy machinery, loaders play a crucial role across construction, mining, and industrial sectors. Among the key systems powering these machines, the loader electrical system stands out as one of the most critical and often overlooked components. A properly functioning electrical system ensures safe operations, system reliability, and extended equipment life. This blog explores the core components, common issues, maintenance tips, and safety considerations related to loader electrical systems.
What is a Loader Electrical System?
The loader electrical system refers to the network of wiring, control modules, sensors, relays, and power sources responsible for running the electrical functions of a loader. These include ignition, lighting, control displays, communication systems, charging systems, and safety alerts. Unlike mechanical issues that are often visible, electrical failures can be subtle, intermittent, and difficult to diagnose—making regular inspection essential.
Key Components of a Loader Electrical System
-
Battery: Acts as the primary power source, especially during start-up.
-
Alternator: Charges the battery and powers the electrical systems while the loader is running.
-
Starter Motor: Responsible for initiating engine rotation.
-
Fuses and Relays: Protect the wiring and prevent overloads.
-
Wiring Harness: Connects various electrical components.
-
Control Modules (ECU/ECM): Control modern automation and communication between systems.
-
Lighting & Indicators: Ensure operational visibility and safety signals.
Understanding these components is essential for anyone involved in the maintenance or operation of loaders.
Common Electrical Issues in Loaders
Several issues can arise in loader electrical systems due to harsh operating environments, age, or poor maintenance. Some of the most common include:
-
Battery failure due to sulfation, corrosion, or low fluid levels.
-
Faulty alternators, resulting in undercharging or overcharging.
-
Corroded or loose wiring, which can cause intermittent power loss.
-
Blown fuses or faulty relays disrupting key systems.
-
Sensor malfunctions leading to incorrect readings or warning signals.
Detecting these problems early can prevent costly downtime and ensure operator safety.
Preventive Maintenance Tips for Loader Electrical Systems
Regular maintenance of the loader electrical system can greatly reduce breakdowns and prolong equipment life. Here are key practices:
1. Scheduled Inspections
Conduct regular visual inspections of wires, battery terminals, and connectors. Look for signs of corrosion, fraying, or loose fittings.
2. Battery Care
Clean battery terminals, check fluid levels, and ensure the battery is properly secured. Use a multimeter to test voltage levels.
3. Check Lighting & Displays
Make sure all work lights, warning indicators, and control displays are operational before each shift.
4. Monitor Charging System
Test the alternator output and ensure the drive belt is in good condition and tensioned correctly.
5. Protect Electrical Connections
Use dielectric grease on terminals and ensure all electrical components are sealed to prevent moisture ingress, especially in dusty or wet environments.
Importance of Qualified Technicians
Though daily checks can be performed by operators, diagnosing and repairing loader electrical systems often requires skilled technicians with specialised diagnostic tools. Investing in regular professional service reduces the risk of misdiagnosis and ensures that complex systems like ECUs and CAN bus networks are maintained correctly.
Loader Electrical System and Safety
Electrical failures can have serious consequences. Faulty systems can disable warning indicators, emergency shutdown systems, or lighting, putting the operator and crew at risk. Therefore, the loader electrical system should be treated as a critical safety component. Implementing safety protocols such as lockout-tagout (LOTO) during repairs, using insulated tools, and adhering to OEM service guidelines is vital during electrical maintenance tasks.
Upgrading Loader Electrical Systems
With technology evolving, many operators are choosing to retrofit older loaders with modern electrical upgrades. These may include:
-
GPS and telematics integration
-
Advanced lighting systems
-
Battery management systems
-
Digital control interfaces
Upgrades not only improve operational efficiency but also reduce long-term maintenance costs.
Conclusion
The loader electrical system is the heartbeat of many essential functions in your equipment. Ignoring it can lead to operational downtime, increased maintenance costs, and safety risks. By understanding its components, identifying early warning signs, and adopting a proactive maintenance approach, you can ensure your loader remains efficient, safe, and productive for years to come.
What's Your Reaction?


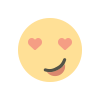



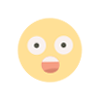