From Compliance to Confidence: How HACCP Strengthens India's Biopharma Ambitions
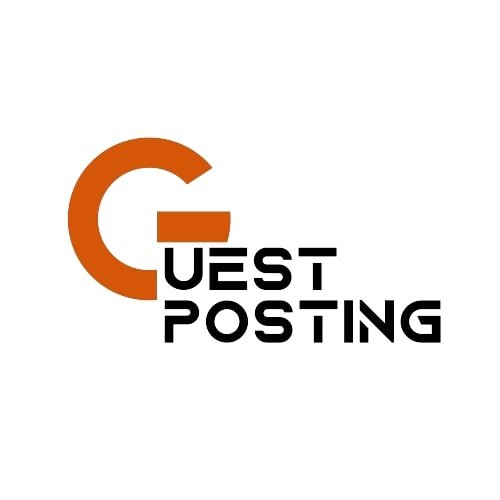
From Compliance to Confidence: How HACCP Strengthens India's Biopharma Ambitions
India’s biopharmaceutical industry is expanding at a global scale, playing a crucial role in healthcare advancements and medicine accessibility. To match international safety standards, Indian manufacturers are increasingly adopting Hazard Analysis and Critical Control Points (HACCP)—a preventive, systematic safety approach that’s become a cornerstone for modern biopharma operations.
In the context of Make in India and Atmanirbhar Bharat, HACCP serves as more than just a compliance framework. It is a catalyst for global credibility, local innovation, and operational excellence.
Why HACCP is Critical in Indian Biopharmaceutical Manufacturing
Biopharmaceutical products require strict controls because they involve complex biological processes. The potential risks—ranging from biological to chemical and even physical contaminants—can compromise safety if not meticulously managed.
HACCP was designed to prevent these risks rather than detect them after the fact. It works by identifying potential hazards at every stage of the production cycle and setting up strict controls to eliminate or reduce these threats.
As manufacturers across India commit to higher quality standards, HACCP is becoming a fundamental part of facility design, production protocols, and quality assurance mechanisms. This shift supports India’s broader ambition of becoming a global manufacturing leader in life sciences.
Explore the detailed study on HACCP adoption in India here.
Supporting Make in India and Atmanirbhar Bharat
The government’s Make in India initiative calls for India to become a world-class manufacturing hub, while Atmanirbhar Bharat emphasizes self-reliance. In biopharma, this translates to high-quality production that earns international trust.
HACCP implementation helps in:
- Strengthening India’s export potential
- Reducing the risk of regulatory rejections
- Enhancing global perception of Indian products
By aligning with international best practices, India’s manufacturing units are evolving from local suppliers to global partners—offering products that match the highest safety standards.
The Seven Principles of HACCP in Biopharma
HACCP follows a structured seven-step system. Each step is crucial for safeguarding product integrity:
- Hazard Analysis
This step involves identifying all potential hazards in the production process. It includes evaluating ingredients, processing methods, and environmental factors that might introduce risks.
- Identification of Critical Control Points (CCPs)
CCPs are specific stages in the production process where controls can be applied to eliminate or reduce hazards. These could include sterilization points, pH balancing steps, or filtration stages.
- Establishing Critical Limits
Each CCP is assigned a critical limit—a value or condition such as temperature or pressure that must be maintained to ensure safety.
- Monitoring Procedures
To ensure critical limits are consistently met, monitoring systems are established. These might include real-time sensors or manual log entries.
- Corrective Actions
If monitoring reveals a deviation from the critical limits, predefined corrective actions are triggered. These ensure the product either returns to a safe state or is discarded appropriately.
- Verification
Regular internal audits and inspections are conducted to validate the effectiveness of the HACCP system and ensure regulatory standards are met.
- Record Keeping and Documentation
Comprehensive documentation ensures traceability and transparency. Every action, check, and correction is recorded for accountability and audit readiness.
Strengthening Compliance Through Cross-Functional HACCP Teams
A key to successful HACCP implementation is forming cross-functional teams. These teams typically include professionals from quality assurance, production, microbiology, and facility management.
Their responsibilities include:
- Performing hazard analysis
- Updating HACCP plans in response to regulatory changes
- Coordinating employee training
- Conducting internal audits
- Ensuring documentation integrity
This collaborative approach ensures that safety becomes a shared responsibility across departments, not just the job of quality control teams.
Overcoming Implementation Challenges
Despite the benefits, some biopharmaceutical companies face challenges with HACCP adoption. These include:
- Complex regulatory procedures
- High cost of compliance
- Lack of trained personnel
- Documentation overload
To tackle these issues, industry leaders are recommending:
- Simplified regulatory interpretations
- Government-supported training initiatives
- Integration of digital platforms for monitoring and record-keeping
These strategies reduce compliance burdens and make it easier for facilities of all sizes to implement HACCP effectively.
Why Frequent HACCP Reviews Matter
The biopharma industry is dynamic, with changing regulations, evolving pathogens, and emerging technologies. As such, HACCP plans must be living documents, reviewed and updated regularly.
Facilities often revise their plans in response to:
- Changes in raw material suppliers
- Process modifications
- Updated regulatory guidelines from authorities like CDSCO or FDA
These reviews help maintain continuous compliance and allow companies to stay ahead of potential safety concerns.
The Digital Shift: Modernizing HACCP Systems
A growing number of Indian companies are adopting digital documentation systems to manage their HACCP programs. These platforms offer:
- Real-time monitoring dashboards
- Cloud-based storage of compliance records
- Automated alerts for deviations
- Easy access during inspections
Digitization supports both efficiency and transparency, reducing human error while enhancing regulatory preparedness.
This move also complements India’s Digital India push, marrying traditional manufacturing with modern tech to create a smart biopharma ecosystem.
Building Global Trust with Every Batch
The global pharmaceutical market is competitive. One mistake can cost a company its reputation. With HACCP, Indian biopharma manufacturers are sending a clear message to international regulators and buyers: We’re serious about quality.
By embedding preventive safety into their core operations, companies:
- Gain faster regulatory approvals
- Reduce the chance of recalls
- Earn long-term customer confidence
This level of trust is essential to expanding India’s role in global supply chains, especially as more countries look for reliable alternatives to traditional suppliers.
Learn more about how HACCP is shaping this trust in Indian biopharma here.
Regulatory Support is Key to Sustained Growth
While industries play their part, regulatory bodies must also adapt. There is a growing need for:
- Flexible, risk-based regulations
- Government-funded HACCP training modules
- Industry-friendly audit procedures
Such support will not only boost compliance but also promote innovation and allow smaller manufacturers to step into the global arena.
Conclusion: HACCP is the Engine Behind India’s Biopharma Rise
HACCP is more than a regulatory checkbox—it is the engine driving India’s emergence as a biopharmaceutical leader. It allows manufacturers to meet global expectations while supporting the national vision of self-reliance.
By prioritizing hazard prevention, record-keeping, and staff training, Indian facilities are setting a new standard in operational excellence. With continued investment, regulatory evolution, and industry commitment, HACCP will help shape an India that’s not just self-reliant, but globally respected.
???? Bibliography
Dhiman, K., & Dadwal, N. (2025). Implementation of hazard analysis and critical control points (HACCP) in Indian biopharmaceutical industries: A field study. Environment Conservation Journal, 26(1), 84–90. https://doi.org/10.36953/ECJ.28512885
What's Your Reaction?


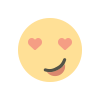



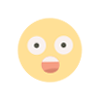