Revolutionizing Workshop Precision: The Rise of the Flexible Arm Tapping Machine

Introduction: The Future of Tapping is Flexible
A Flexible Arm Tapping Machine is quickly becoming the cornerstone of modern manufacturing and mechanical workshops. With increasing demand for speed, accuracy, and operator safety, traditional tapping setups are being replaced with smarter, more ergonomic solutions. Enter the flexible arm — a game-changer in the world of tapping operations.
Today, tapping doesn’t just require force—it requires finesse. From minimizing operator fatigue to maximizing tapping consistency, flexible arm tapping machines offer a dynamic solution fit for industries that prioritize productivity and precision. If you’re aiming to upgrade your tapping capabilities, this article will walk you through everything you need to know about why flexible arm systems are redefining the standard.
The Evolution of Tapping: A Quick Look Back
Before diving into why flexible arm tapping machines are so effective, it’s essential to understand where we came from. Tapping, the process of cutting threads inside holes, has long been a manual or semi-automated task. Operators would rely on hand-held taps or bulky machines with limited mobility.
However, as industrial demands rose and products became more complex, manufacturers started looking for better solutions. The early tapping machines lacked the ergonomic design and flexibility we see today. Over time, the need for accuracy, speed, and safe operations led to innovations that birthed the flexible arm tapping machine.
This evolution was not just a technological upgrade—it was an ergonomic revolution. The flexible arm made it easier for operators to handle multiple tapping angles, drastically reducing setup time and error rates.
Why Flexible Arm Tapping Machines Are the New Standard
What sets the flexible arm tapping machine apart from its predecessors is its ability to move freely in multiple directions while maintaining tapping precision. These machines can be mounted on a bench or floor and are typically powered by pneumatic or electric motors.
The biggest advantage is that the flexible arm absorbs the torque of the tapping process, reducing operator strain and making the process much smoother. This design promotes a seamless workflow, especially in high-volume production environments. It’s no surprise that more and more workshops are shifting toward these machines to stay competitive.
Key Features That Define Performance
Modern flexible arm tapping machines are engineered with features that prioritize precision and ease of use. Most models come with torque control, depth stop systems, and auto-reverse mechanisms. These features ensure consistency in thread quality while minimizing the risk of over-tapping or thread damage.
Another notable feature is adjustable speed control. Operators can fine-tune the tapping speed based on the material, whether it’s aluminum, steel, or plastic. This not only improves efficiency but also extends the life of the tapping tools, leading to long-term cost savings.
Benefits That Make a Big Difference
The benefits of flexible arm tapping machines go beyond just mechanical performance—they contribute to a more ergonomic and efficient workspace. Firstly, these machines reduce the physical effort required from operators. Since the arm bears the weight and torque, users can work longer without fatigue.
Secondly, productivity receives a massive boost. With quicker setups and easy mobility, tapping cycles become faster. And because there’s less human error involved, the quality of threads remains consistently high. In industries where time is money, this kind of productivity edge is invaluable.
Ideal Applications Across Industries
Flexible arm tapping machines are highly versatile and can be used across multiple sectors. In the automotive industry, they’re often used to create threaded holes in engine components and brackets. The aerospace industry also values them for tapping lightweight, high-strength alloys with precision.
Even in furniture manufacturing, these machines assist in threading holes for metal fittings in wood or composite materials. Their versatility allows them to fit seamlessly into any assembly line or standalone workstation.
Whether you're tapping soft materials or hard metals, these machines can be adapted to meet the specific requirements of your job. That’s what makes them a worthy investment for modern workshops.
Installation and Operation: Simplicity Meets Efficiency
Setting up a flexible arm tapping machine is a relatively straightforward process. Most units are delivered pre-assembled and can be mounted on workbenches or mobile stands. Once secured, they require only a power source—either pneumatic or electric—and they’re ready to go.
Operating the machine is equally intuitive. With adjustable arms and rotation stops, the machine can be positioned exactly where needed. Torque settings, tapping speed, and direction are easily controlled via user-friendly interfaces. This makes training new operators simple and fast.
Moreover, most models are low-maintenance and come with safety systems to protect both the equipment and the user during operation.
Safety and Ergonomics: A Better Work Environment
One of the most significant contributions of flexible arm tapping machines is their impact on workplace safety and ergonomics. Traditional tapping methods often led to repetitive strain injuries due to the forceful twisting motion. Flexible arm systems eliminate this risk by distributing the load away from the operator.
Additionally, these machines come with features like anti-rotation locking and overload protection. These functions ensure that even in the event of a malfunction or tough material, the operator remains protected. This emphasis on safety not only protects workers but also reduces downtime due to injury.
When it comes to ergonomic design, flexible arm machines lead the way. They’re built to adjust to the operator’s height and reach, allowing for natural movements and reducing strain throughout the workday.
How to Choose the Right Model
Choosing the right flexible arm tapping machine involves evaluating your production volume, material types, and workspace layout. For small workshops, compact bench-mounted models may be ideal. For larger-scale operations, floor-mounted systems with extended arm reach may be more suitable.
Other considerations include torque requirements, tapping speed, and thread sizes. Always opt for models that offer versatility—machines that can be easily adapted to different tasks will provide the most value over time.
Make sure to check the build quality and support service offered by the supplier. At Ravisons Corporation, you’ll find a wide range of customizable options tailored for different industrial needs. Ravisons is among the trusted Tapping Machine Suppliers known for reliability, innovation, and robust post-sale support.
Conclusion: Elevate Your Workshop With Smarter Tapping Solutions
Flexible arm tapping machines are no longer a luxury—they’re a necessity for workshops aiming to keep up with modern demands. With their unmatched versatility, ergonomic design, and consistent output, these machines are transforming how industries approach tapping operations.
Whether you’re a small fabricator or a large manufacturer, upgrading to a flexible arm tapping machine is a step toward greater efficiency and higher precision. At Ravisons Corporation, innovation meets practicality to deliver solutions that truly work for you.
If you’re looking to streamline your tapping process while improving safety and quality, a flexible arm tapping machine is the upgrade your operation needs.
What's Your Reaction?


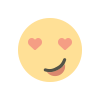



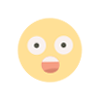