Soft Jaws Explained: Benefits, Materials, and Applications
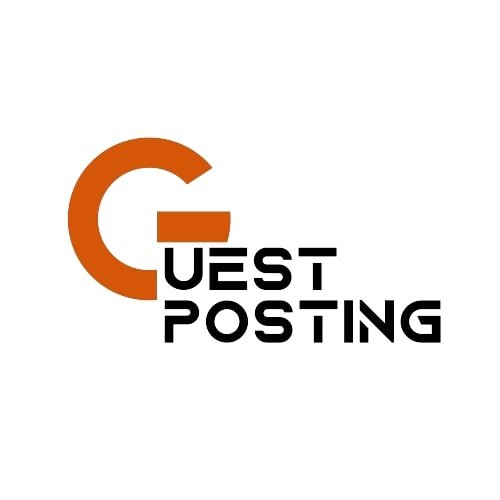
Introduction: Why Soft Jaws Matter in Machining and Clamping
In the world of precision machining, securing a workpiece properly is one of the most important steps to achieving accurate, repeatable results. Whether you're shaping metals, plastics, or delicate components, one small shift in position can cause major errors or costly damage. That’s where soft jaws come in.
Soft jaws are essential in clamping setups when precision and surface protection matter. Unlike hard jaws, which are made for strength and durability, soft jaws are built for flexibility and care. They can reduce part damage by up to 50%, making them a must-have in industries that work with fragile or irregularly shaped parts.
In this guide, we’ll break down what soft jaws are, their benefits, materials used, where they’re applied, and expert tips for getting the best results.
What Are Soft Jaws?
Definition and Basic Concept
Soft jaws are specially made inserts that go inside the jaws of a chuck, vise, or other workholding tool. They’re usually made from softer materials and are custom-machined to match the shape of the specific part being held. Because of their flexibility, they offer better surface protection and allow for tighter, more secure clamping.
You’ll often find soft jaws used in CNC machines, manual lathes, milling setups, and other high-precision environments. Their job is simple yet critical: hold the part tight without damaging it.
How They Differ from Hard Jaws
Hard jaws are made from steel or hardened alloy and are designed to grip parts firmly with minimal wear over time. They’re best for general use and high-volume production runs. However, they’re not ideal when working with delicate parts or non-metal materials.
Soft jaws, by contrast:
-
Can be reshaped or customized easily for different workpieces.
-
Conform better to odd-shaped or sensitive parts.
-
Provide more even pressure, helping avoid scratches, dents, or misalignment.
Key Features and Design
Soft jaws are:
-
Custom-machined for a specific job or shape.
-
Designed with features like grooves, reliefs, or stops that mirror the workpiece.
-
Made to reduce part movement and improve repeatability.
This customization helps ensure minimal part movement, less vibration during machining, and improved part quality.
Benefits of Using Soft Jaws
Protecting Delicate Materials
One of the biggest reasons to use soft jaws is to protect sensitive or fragile materials. Whether you’re working with:
-
Thin aluminum sheets
-
Polished surfaces
-
Plastics
-
Glass or ceramics
Soft jaws provide a gentler grip that prevents scratches, dents, or cracks. They’re especially useful in industries where the surface finish is critical to performance or appearance.
Improving Clamping Accuracy
Soft jaws are designed to match the exact profile of the part, which means they:
-
Improve contact between the jaw and workpiece.
-
Reduce the risk of slippage during machining.
-
Help maintain tight tolerances and clean edges.
This high level of precision makes them perfect for CNC machining or any application where accuracy is key.
Cost and Time Savings
Soft jaws can be a great investment when it comes to saving time and money:
-
They reduce setup time for repeat jobs since they’re already shaped to fit the part.
-
They lower the risk of damaging expensive parts, which saves material costs.
-
With proper care, soft jaws can be used multiple times, making them economical for small production runs.
Enhancing Safety and Quality
Using soft jaws also helps improve shop safety and overall quality. By holding the part securely, they:
-
Minimize vibration and potential tool damage.
-
Help maintain consistent measurements and finishes.
-
Prevent accidents caused by loose or shifting workpieces.
Materials Used for Soft Jaws
Common Materials
The material you choose for soft jaws depends on the job. Some common materials include:
-
Aluminum: Lightweight, easy to machine, and good for light-duty clamping. Often used in prototypes and soft material machining.
-
Copper and Brass: Soft, non-marring metals ideal for delicate surfaces or polished parts.
-
Soft Steel (Low Carbon Steel): Offers a balance of strength and flexibility. It's a popular choice for general-purpose applications and can be reused after machining.
Special Materials and Coatings
For even more delicate applications, shops use coated or composite materials like:
-
Polymer-coated jaws: Excellent for protecting high-value or polished parts.
-
Rubber or Silicone Inserts: Provide extra grip and cushioning in fragile or high-vibration setups.
These specialty jaws are often used in medical, aerospace, or electronic applications where precision and protection are non-negotiable.
Choosing the Right Material
When selecting the material for soft jaws, ask yourself:
-
What is the workpiece material? (Metal, plastic, ceramic?)
-
How much clamping force will be applied?
-
What surface finish or tolerance must be preserved?
-
How often will the jaws need to be replaced or re-machined?
Balancing these factors ensures your jaws perform well and last longer without damaging the part.
Applications of Soft Jaws in Industry
Soft jaws are used in many industries that require precision, surface protection, or custom workholding. Here are a few examples:
Precision Machining and Manufacturing
Soft jaws are frequently used in CNC machining centers to hold parts that require multiple operations. For instance:
-
Automotive parts such as brake components or engine covers that need precise alignment.
-
Tool and die making, where small changes in positioning can ruin the whole mold.
Medical Device Manufacturing
Medical parts, like:
-
Sensors
-
Implants
-
Surgical tools
...must be clamped securely without scratching or altering surface coatings. Soft jaws help maintain the integrity and functionality of these critical components.
Jewelry Making and Watchmaking
In industries where appearance and fine detail matter, soft jaws are indispensable. Jewelers and watchmakers use them to:
-
Hold tiny or fragile parts securely.
-
Avoid marring soft metals like gold or silver.
-
Make precise adjustments without causing damage.
Aerospace and Defense
Aerospace parts often have complex geometries and tight tolerances. Soft jaws allow manufacturers to:
-
Clamp irregular parts safely.
-
Avoid deformation during multi-step machining processes.
-
Maintain critical tolerances for components used in flight systems.
Expert Tips and Best Practices
To get the best results from soft jaws, follow these expert recommendations:
-
Customize Jaws for Each Job
Don’t reuse jaws across different parts unless they match closely. Customize each set for a perfect fit. -
Inspect for Wear and Damage
Over time, jaws can deform or wear down. Regularly check for dents, grooves, or debris buildup. -
Control Clamping Pressure
Use the minimum pressure needed to hold the part securely. Over-tightening can crush the part or deform the jaws. -
Keep Detailed Records
Label and log modified jaws for future reuse. Keep notes on material type, part specs, and machine settings for repeat jobs. -
Clean Before Use
Always wipe down jaws and the workpiece before setup. Clean surfaces reduce slippage and ensure more accurate clamping.
Conclusion: The Power of Soft Jaws in Achieving Better Results
Soft jaws are more than just workholding accessories—they are a key to improving precision, efficiency, and quality in machining operations. By choosing the right material, customizing the design, and applying proper use and care, you can dramatically reduce part damage, increase repeatability, and save time on every job.
Whether you're machining aerospace parts, assembling medical devices, or polishing fine jewelry, soft jaws offer the perfect balance of grip and gentleness. Investing in high-quality soft jaws can lead to better results, fewer mistakes, and longer-lasting parts—making them an essential tool in any modern workshop.
What's Your Reaction?


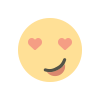



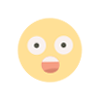