What Are Digital Twins and Why Are They Important for Logistics?
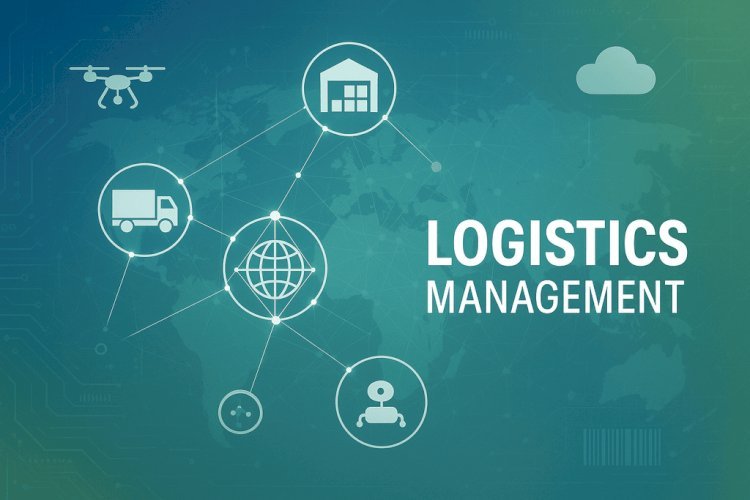
Why Are Digital Twins Transforming Logistics in 2025?
Let me take you back to a warehouse I once walked through years ago. Forklifts moved with an urgency that didn’t match the inefficiency I saw. Shelves were jammed. Staff fumbled with paper checklists. It looked like a machine running with missing bolts.
Now imagine that warehouse today—but with its digital twin running side-by-side in real time. No guesswork. Just data-fed simulations predicting what’ll go wrong and when. That’s not sci-fi. That’s 2025.
Digital twins are virtual replicas of physical logistics assets—your warehouse floors, delivery fleets, even forklift patterns. They enable real-time monitoring, simulation, and decision-making. In this era of e-commerce chaos, where a 15-minute delay costs thousands, digital twins are becoming non-negotiable.
They’re the clean processes we’ve been preaching for years—digitized. And for anyone managing logistics in 2025, there’s no excuse for flying blind.
What Is a Digital Twin?
Hey friends ????, a digital twin is basically a real-time, data-driven digital model of a physical object or system.
In logistics, this means simulating operations—like how packages move through a warehouse or how trucks run delivery routes. These twins don’t just observe; they think, they predict, and they help us prevent problems before they occur.
Why Are They Gaining Traction?
The driving force? IoT sensors, AI, and the overwhelming demand for efficiency.
Companies like DHL launched digital twin pilots in 2025 to simulate warehouse flows and improve fulfillment speed. With sensors feeding live data and AI predicting outcomes, the digital twin isn’t just a dashboard—it’s an intelligent assistant.
How Do Digital Twins Optimize Warehouse Operations?
Back in the day, warehouses were managed by tribal knowledge—Frank knew where stuff was, so you asked Frank. That’s operational debt at its worst.
Today, digital twins simulate entire warehouse ecosystems. From shelf layout to robot movements, everything is tested virtually before being applied physically. That’s craftsmanship—building before you build.
By modeling different workflows, digital twins reduce chokepoints, enhance picking efficiency, and prevent human error. In a logistics management system, that means fewer wrong picks, less inventory loss, and shorter cycle times.
For 2025, this simulation-first approach has become essential—especially in high-volume e-commerce where even a 1% delay snowballs fast.
How Are Warehouses Simulated?
Picture this: Every robot, conveyor, and worker in your warehouse has a sensor feeding data into a 3D digital model.
That’s how companies like Amazon now simulate picking routes using digital twins. They model optimal picking paths, simulate them in real time, and update layouts instantly. IoT and robotics aren’t just accessories—they’re the raw inputs for your twin.
Why Do They Reduce Bottlenecks?
Friends, imagine a traffic jam that hasn’t happened yet—but your system predicts it and reroutes before it forms. That’s what predictive analytics inside a digital twin does.
In 2025, warehouses using these simulations have cut processing delays by 25%. Why? Because digital twins simulate where congestion will occur based on volume, movement, and flow data—and help you fix it ahead of time ????.
How Do They Enhance Inventory?
Inventory inaccuracy is the silent killer of logistics. Digital twins integrate real-time data from RFID, barcodes, and shelf sensors to track stock precisely.
Blue Yonder’s implementation in 2025 showed how digital twins boosted inventory accuracy by reducing mismatches and shrinkage. Real-time visibility isn’t just cool—it’s a requirement in the best logistics software.
How Do Digital Twins Improve Fleet Performance?
Now let’s move from the warehouse floor to the open road ????.
Managing fleets isn’t just about knowing where your trucks are. It’s about knowing how they’re performing, predicting failures before they happen, and optimizing routes for both time and fuel.
Digital twins simulate fleet behavior—from engine performance to traffic conditions. In 2025, this means smarter routing, fewer breakdowns, and faster last-mile deliveries.
UPS, for instance, isn’t just tracking trucks—they’re simulating their entire journey in advance to minimize hiccups. That’s professional discipline in top logistics software.
How Are Fleets Simulated?
Fleet twins use GPS, telematics, and vehicle sensor data to create a constantly updated model of each vehicle.
UPS, in 2025, uses these twins to map optimal routes based on weather, traffic, and fuel use. Instead of reacting to traffic, they’re avoiding it altogether. Clean routing equals clean delivery performance.
Why Is Maintenance Prediction Valuable?
Every unplanned breakdown is operational debt. With digital twins, maintenance becomes predictive.
Fleet twins analyze engine vibrations, fuel efficiency trends, and usage patterns to schedule maintenance before failure. The result? Downtime slashed by 20% in 2025. That’s not a guess—that’s from real deployments.
What Technologies Power Digital Twins?
Okay guys, let’s break it down. Digital twins don’t run on magic—they run on a trio of tech craftsmanship: IoT and AI in Logistics, and cloud computing.
These systems gather massive amounts of data, crunch it in milliseconds, and output actionable insights. You’re not just watching things unfold—you’re engineering logistics precision.
Without these pillars, a twin is just a static model. With them? It becomes a living, breathing simulation.
How Does IoT Enable Twins?
IoT is the nervous system. Sensors on shelves, forklifts, and trucks send constant updates to the twin.
In 2025, Siemens used IoT-enabled devices to power warehouse twins that can detect and correct inefficiencies in real time. It’s like having eyes and ears on every square foot ????.
What Is AI’s Role?
AI is the brain behind the twin. It detects patterns, predicts events, and recommends actions.
Oracle’s AI-driven twins, for example, analyze billions of data points to optimize delivery schedules and warehouse layout in real time. No guesswork—just guided logistics precision.
What Are the Broader Benefits of Digital Twins?
Beyond performance gains, there’s a deeper layer of value here.
Digital twins support sustainability by cutting waste, lowering emissions, and streamlining energy use. They also help simulate disruptions—like strikes, weather delays, or inventory surges—so we’re prepared.
In logistics management software, these simulations are the ultimate safety net.
How Do Twins Support Sustainability?
By optimizing fuel use and energy consumption, digital twins enable logistics systems to reduce carbon footprints.
In 2025, companies are using twins to run green warehouses—predicting energy peaks and minimizing unnecessary usage. The result? Lower utility costs and a cleaner conscience ????.
Why Do They Mitigate Risks?
We can’t stop disruption—but we can simulate it.
Digital twins allow you to test “what if” scenarios. A sudden route closure? Labor shortage? With a twin, you already know the fallback. Companies in 2025 are reporting 30% fewer fulfillment delays thanks to these proactive simulations.
Final Thoughts
Look friends, logistics in 2025 isn’t about reacting anymore—it’s about anticipating. And that means digital twins are no longer optional.
They simulate your warehouses. They optimize your fleets. They cut costs and protect you from surprises.
If you’re managing logistics without one, you’re flying blind in a storm. But with a digital twin? You’re piloting with radar, autopilot, and foresight.
Let’s build systems with discipline, not duct tape.
Key Takeaways
- Digital twins simulate warehouses and fleets, boosting efficiency in 2025.
- Warehouse twins reduce bottlenecks and improve inventory accuracy.
- Fleet twins optimize routes and predict maintenance, cutting costs.
- IoT and AI power real-time, scalable digital twin simulations.
- Twins enhance sustainability and risk mitigation for competitiveness.
Frequently Asked Questions (FAQs)
1. What Are Digital Twins in Logistics?
Digital twins in logistics are virtual models that represent real-world operations like warehouses or vehicle fleets. They use live data from sensors to simulate and optimize processes, helping improve efficiency, reduce downtime, and ensure accurate forecasting in logistics workflows.
2. How Do They Optimize Warehouses?
Digital twins optimize warehouses by simulating layouts, robotic movement, and inventory flow. They identify inefficiencies and bottlenecks in real time. By adjusting configurations based on data, they help improve storage use, picking accuracy, and overall warehouse throughput.
3. Why Are Fleet Twins Important?
Fleet digital twins simulate vehicle behavior using GPS and engine data. They optimize delivery routes, monitor vehicle health, and predict maintenance. This helps companies reduce fuel usage, improve delivery reliability, and minimize costly downtime—especially crucial in last-mile logistics.
4. What Technologies Enable Twins?
Technologies that power digital twins include IoT sensors, AI algorithms, and cloud computing platforms. Sensors collect real-time data, AI interprets patterns, and cloud systems ensure scalable access and simulation. Together, they create a powerful framework for real-time logistics modeling.
5. How Do Twins Benefit Logistics?
Digital twins benefit logistics by increasing operational visibility, enabling predictive maintenance, reducing delays, and enhancing inventory accuracy. They also support sustainability and disaster preparedness, making them vital tools for running efficient, future-ready logistics management systems.
What's Your Reaction?


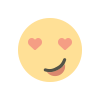



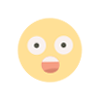